Projekt 2.6
Smelter development for net zero-carbon steelmaking
Einleitung
Die Dekarbonisierung der Stahlindustrie erfordert innovative Lösungen für einen möglichst CO2-armen Stahlerzeugungsprozess mit dem langfristigen Ziel einer Netto-Null-Kohlenstoff-Produktion im Einklang mit dem europäischen Green Deal. Um eine Netto-Null-Kohlenstoff-Stahlerzeugung zu erreichen, ist eine Anpassung der bestehenden integrierten Routen über den Hochofen – Sauerstoffblasofen (BF-BOF) erforderlich. Die wasserstoffbasierte Direktreduktion (DR) ist eine vielversprechende Technologie für die CO2-freie Eisenerzreduktion. Da die Direktreduktion ohne Flüssigphase arbeitet, wird eine Vorschmelze als Bindeglied zwischen der Direktreduktionsanlage und dem Sauerstoffblasofen benötigt, um minderwertiges direktreduziertes Eisen (Direct Reduced Iron = DRI) in Roheisen umzuwandeln, bevor es raffiniert wird. Die Entwicklung dieser Schmelzanlage steht im Mittelpunkt des aktuellen Projekts.
Ziele und Motivation
- Entwicklung von Schmelzöfen unter Berücksichtigung spezifischer Fragen wie Schmelzofengeometrie, geeignete feuerfeste Auskleidung, Schlackenbildung, Aufkohlung von Roheisen usw.
- Bestimmung geeigneter Einsatzstoffe (DRI auf Basis von Pellets, Sinter, Feingut, etc.) und Kohlenstoffträger
- Durchführung von Sensitivitätsanalysen zur Prozessoptimierung (z. B. Kombination von Schmelzofen mit Direktreduktion)
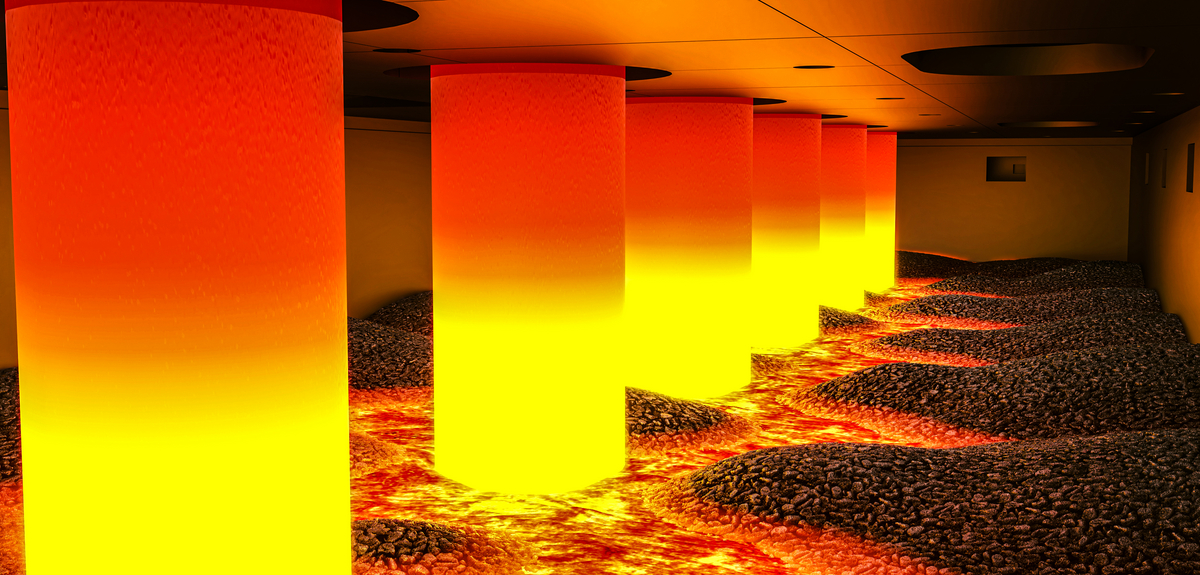
Vorgehensweise
- Theoretische Betrachtung des Schlackenbildungsprozesses mit begleitender thermodynamischer Modellierung (Bildung von Primär- und Endschlacke, Schmelztemperatur)
- Untersuchungen zur elektrischen Leitfähigkeit der Schlacke
- Grundlegende metallurgische Betrachtungen, wie z. B. Metallaufkohlung, Reaktionen im Möller (Kalzinierung, Reduktion) und in der Schlacke innerhalb des Schmelzofens
- Bewertung des Roheisens und seiner Nebenprodukte
- Definition von geeigneten Eisenträgern für den Schmelzprozess (Matrix mit Vor- und Nachteilen unter Berücksichtigung von direktreduziertem Eisen und Eisenschwamm (Hot Briquetted Iron = HBI) auf Basis von Pellets, Sinter oder Feingut)
- Definition und Bewertung von geeigneten Kohlenstoffträgern als Reduktions- und Aufkohlungsmittel
- Untersuchung von Stahlwerksrückständen (Stäube, Schlämme und Zunder), die direkt mit der Schmelze recycelt werden können
- Schmelzversuche im Labormaßstab mit unterschiedlichen Einsatzstoffen und Additiven
- Untersuchung eines möglichen Feuerfestkonzepts für die Schmelzanlage unter Berücksichtigung von Aspekten wie Lebensdauer, Wartungsanforderungen, Beständigkeit gegen Schlacke oder möglicher Schutz durch eine erstarrte Schlackenschicht
- Festlegung einer geeigneten Schmelzofengeometrie
- Bewertung kritischer Elemente wie Zink oder Alkalien im Falle von Zyklen und Anreicherung im Prozess
- Sensitivitätsanalysen des Schmelzprozesses unter Berücksichtigung von Kombinationen mit einer Direktreduktionsanlage zur Festlegung möglicher Betriebspunkte mit Schwerpunkt auf Parametern wie Metallisierungsgrad, Kohlenstoffgehalt des direktreduzierten Eisens usw.
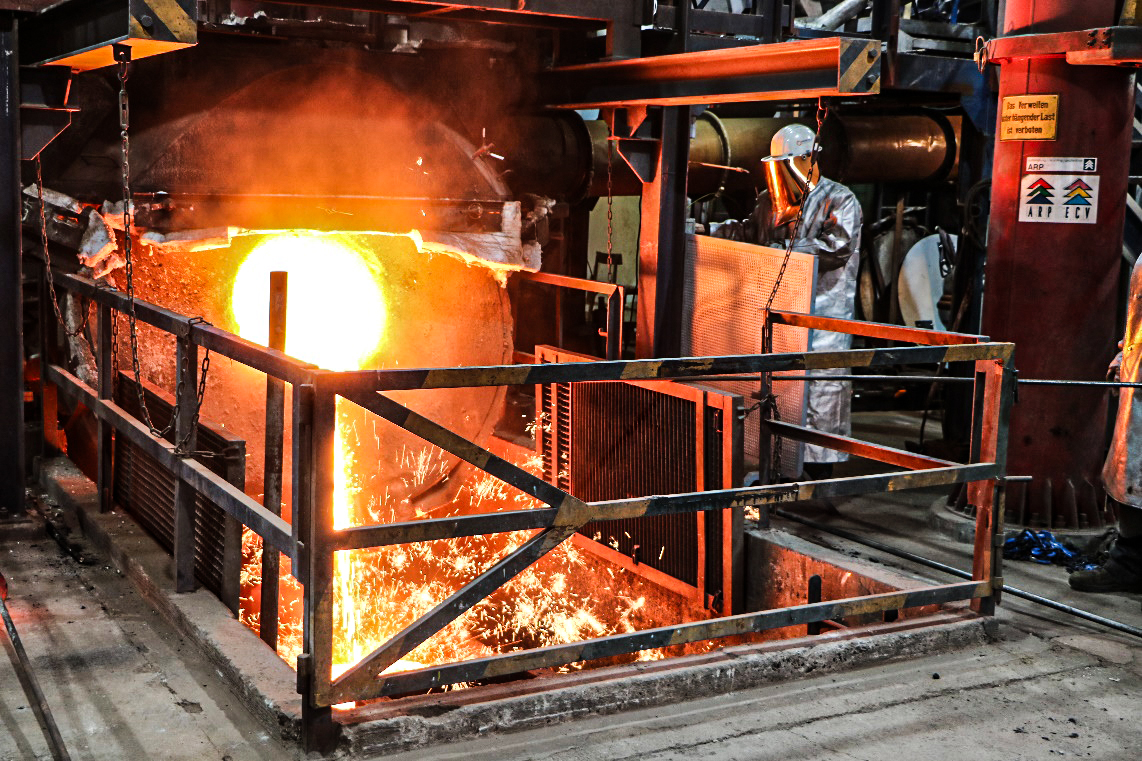
Ergebnisse und Anwendung
Es werden grundlegende metallurgische Kenntnisse über die Schmelzmasse der Reaktionen sowie Kenntnisse über den Schlackenbildungsprozess und die Eigenschaften der Primär- und Endschlacke erworben. Das Aufkohlungsverhalten des Metalls, die Gasausnutzung und die Eigenschaften des Roheisens und seiner Nebenprodukte werden ermittelt.
Darüber hinaus werden geeignete Eisenträger für die Schmelzanlage ermittelt und Kenntnisse über Kohlenstoffträger (Alternativen zum Hüttenkoks), ihre Eigenschaften und ihre Auswirkungen auf den Schmelzprozess gewonnen. Die Anforderungen an die chemischen und physikalischen Eigenschaften von Stahlwerksrückständen für das Recycling werden festgelegt.
Die Auswirkungen von alternativen Eisen- und Kohlenstoffträgern auf die Schmelzleistung werden quantifiziert. Kenntnisse über die zu erwartenden Produktqualitäten (Roheisen, Schlacke) und grundlegende Informationen über die Schmelzofengeometrie werden verfügbar sein. Es wird ein geeignetes Konzept für die Feuerfestauskleidung der Schmelzanlage erstellt. Mögliche Schmelzbetriebspunkte und daraus abgeleitete Trends für die zu erwartende Produktivität, Ausbeute und CO2-Emissionen werden verfügbar sein.
Die endgültige Roheisen- und Schlackenzusammensetzung mit Schwerpunkt auf dem Kohlenstoff-, Silizium-, Mangan-, Schwefel- und Phosphorgehalt soll bewertet werden. Die Abgaszusammensetzung wird definiert und die Eignung des Roheisens und der Nebenprodukte für die Weiterverarbeitung in verschiedenen Aggregaten wird analysiert.