Projekt 2.3
Carbonatisation
Einleitung
Das Projekt befasst sich mit Nebenprodukten (Aschen, Schlacken) aus der Zement- und Feuerfestproduktion sowie aus dem Stahlwerk, die auf eine geeignete Partikelgröße gemahlen und direkt mit CO2 aus diesen energieintensiven Industrien karbonisiert werden. Das bedeutet, dass diese Nebenprodukte verwendet werden, um CO2 in fester Form zu binden Die dabei entstehenden Karbonate werden deponiert. Da diese Nebenprodukte ohnehin deponiert werden müssen, stellt diese Methode eine Alternative zu den üblichen Szenarien von Carbon Capture and Storage (CSS) dar.
Der Karbonatisierungsprozess wird mit gereinigtem CO2 aus der energieintensiven Industrie wie der Feuerfestproduktion oder der Stahlindustrie, aber auch mit unbehandelten Abgasen durchgeführt.
Im Rahmen eines früheren K1-MET-Projektes (P 1.2 Utilization of metallurgical slags, 2019 – 2023) wurde an der Montanuniversität Leoben (Lehrstuhl für Aufbereitung und Veredlung) eine Druck-Attritionsmühle/Reaktor zur Nassbehandlung von LD-Schlacke mit CO2 bis zu 60 bar eingesetzt. Die gewonnenen Erfahrungen werden für die tiefgreifende Entwicklung einer containerbasierten Pilotanlage genutzt, die entsprechend den Anforderungen der Abfallstoffe, die von den im Prozess Beteiligten bereitgestellt werden, betrieben wird.
Darüber hinaus zielt das zu entwickelnde Verfahren darauf ab, den Gesamtenergiebedarf sowie die Systemkomplexität zu verringern, um einen wirtschaftlich und ökologisch sinnvollen CCS-Prozess zu erreichen.
Ziele und Motivation
- Bestimmung der optimalen Prozessbedingungen
- Untersuchung der erforderlichen Partikelgrößen
- Bewertung des Einflusses verschiedener Sekundärrohstoffe auf den Karbonatisierungsprozess
- Konstruktion und Betrieb einer Pilotanlage zur direkten Karbonatisierung geeigneter Aschen und Schlacken in der Umgebung einer Zementproduktionsanlage
- Kombination des Mahlprozesses mit der Karbonatisierungsreaktion in einem Apparat, um die Umwandlungsrate und die Ausbeute an Karbonaten zu erhöhen
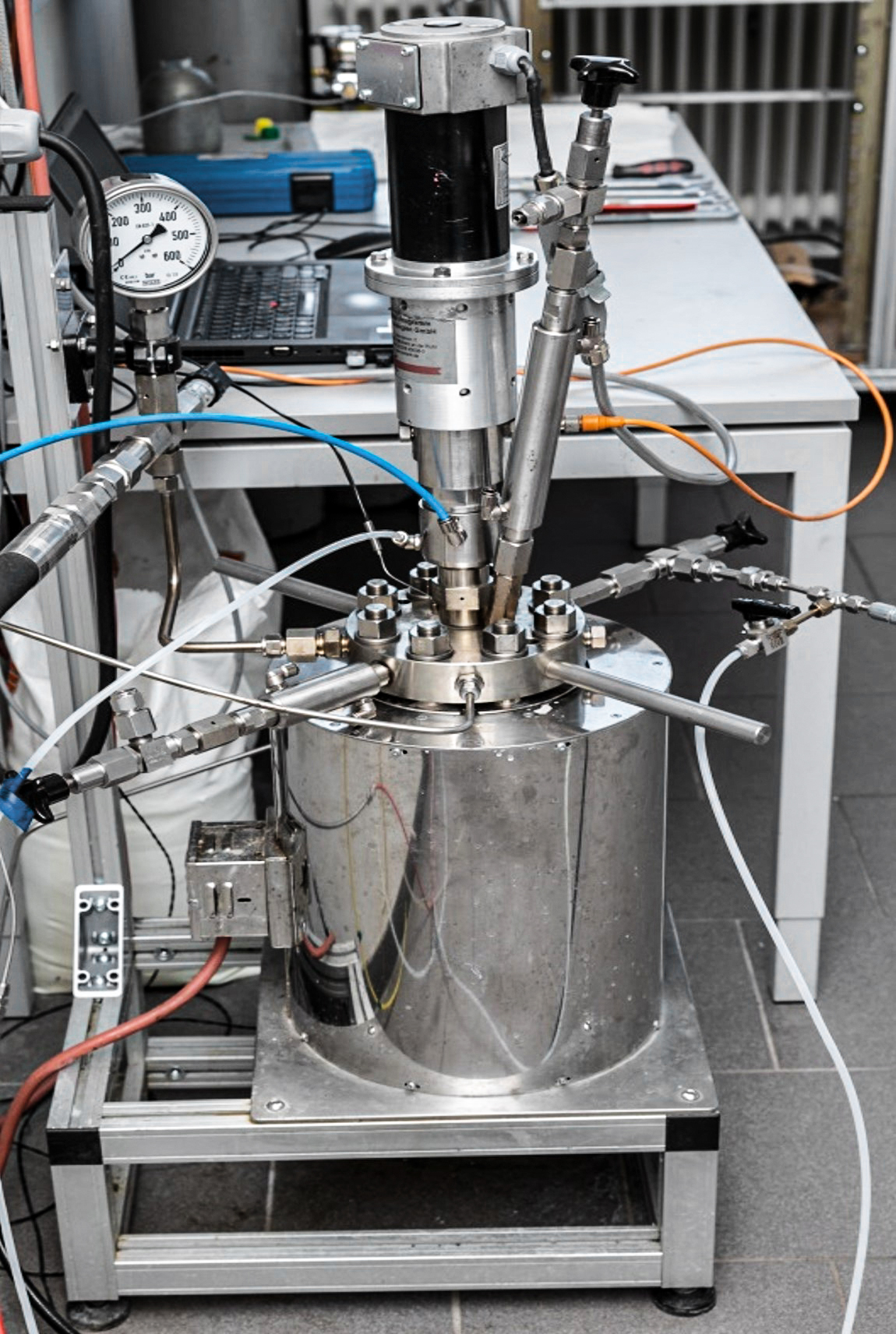
Vorgehensweise
- Umfassende Literaturrecherche zu direkten Karbonatisierungsverfahren, verwendeten Rohstoffen, eingesetzten Apparaten und Betriebsbedingungen, um geeignete Bedingungen für Laborexperimente zu ermitteln
- Laborexperimente zur systematischen Untersuchung des Einflusses der verschiedenen Sekundärrohstoffe, der Partikelgröße und der Betriebsbedingungen (Temperatur, Druck, CO2-Partialdruck, Verweilzeit) auf Geschwindigkeit und Ausbeute
- Charakterisierung der Rohstoffe sowie der Produkte aus dem Karbonatisierungsprozess mittels Rasterelektronenmikroskopie – Energiedispersive Röntgenspektroskopie (SEM-EDX) sowie Thermogravimetrische Analyse – Differenzkalorimetrie (TGA-DSC)
- Konstruktion und Betrieb eines kombinierten Mahl- und Reaktivapparates im Pilotmaßstab unter den im Labormaßstab ermittelten vielversprechendsten Bedingungen
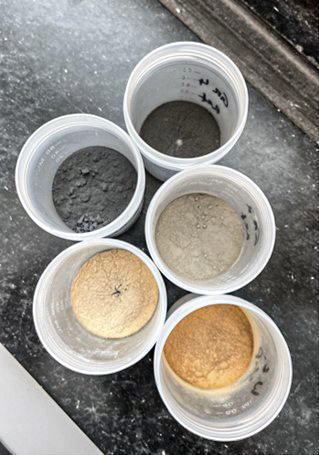
Ergebnisse und Anwendung
Im Rahmen des Projekts wird eine Apparatur für ein kombiniertes Mahl- und reaktives Karbonatisierungsverfahren entworfen. Es werden optimale Betriebsbedingungen für den direkten Karbonatisierungsprozess unter Berücksichtigung von Umwandlungsraten und Ausbeuten bestimmt. Außerdem werden verschiedene Sekundärrohstoffe auf ihre Eignung für den Karbonatisierungsprozess untersucht. Erste Abschätzungen der Betriebskosten (OPEX) und der Investitionskosten (CAPEX) für einen industriellen Karbonatisierungsprozess werden durchgeführt. Es werden Massen- und Energiebilanzen erstellt und das Potenzial für die CO2-Reduktion abgeschätzt.