Projekt 2.1
Continuous hydrogen plasma smelting reduction process development
Einleitung
Die Pilotanlagenversuche für die Wasserstoff-Plasma-Schmelzreduktion (HPSR) zeigten ein durchführbares Konzept, und die ersten Prozessdaten bestätigten eine Weiterentwicklung. Nichtsdestotrotz sind weitere Anpassungen der Anlagenausrüstung und die Implementierung zusätzlicher Messgeräte erforderlich, um genügend Daten für ein gut konzipiertes und fundiertes Scale-up zu sammeln.
Da der HPSR-Prozess ohne den Einsatz von Kohlenstoffträgern zur Reduktion arbeitet, wird erwartet, dass sich die Schmelze (Eisen und Schlacke) von dem Produkt des industriell angewandten Prozesskonzepts Hochofen + Basissauerstoffofen unterscheidet. Daher muss die sekundärmetallurgische Behandlung für die Produkte des HPSR-Verfahrens neu definiert werden.
Aufgrund des Einflusses von Design und Anordnung der elektrischen Ausrüstung sind weitere Untersuchungen notwendig, um die besten Bedingungen für einen stabilen Prozess zu erreichen. Darüber hinaus ist die Rückgewinnung von Wasserstoff im Abgas für den wirtschaftlichen Erfolg des Prozesses von entscheidender Bedeutung. Darüber hinaus werden Labor- und Pilotanlagenversuche dazu beitragen, die Bedingungen in den verschiedenen Prozesszonen (Schlacke, Metall, Gas) zu simulieren. Dies sollte zu den praktikabelsten und ökologischsten Prozessbedingungen führen.
Ziele und Motivation
- Neudefinition der sekundärmetallurgischen Behandlung für die Produkte des HPSR-Verfahrens.
- Einführung und Reduktion von oxidischen Legierungselementen
- Untersuchung der Herstellung von Ferrolegierungen wie Ferrochrom
- Bestimmung des Schwefel- und Phosphorgehalts und deren Verteilung in den verschiedenen Phasen des Prozesses
- Realisierung und Untersuchung eines semikontinuierlichen Betriebs der installierten Pilotanlage
- Zusammenführung aller experimentellen Ergebnisse und Erkenntnisse zum Einstieg in das Basic-Engineering einer großtechnischen, wirtschaftlicheren Pilotanlage für den kontinuierlichen Betrieb
- Erstellung einer CFD-MHD-Simulation des HPSR-Reaktors, die die physikalischen Prozesse in der entsprechenden Reaktorgeometrie abbildet
- Entwicklung und Einbindung der Reaktionskinetik, chemischen Wechselwirkungen und Thermodynamik des Wasserstoffplasmas sowie des Lichtbogens in die Simulation
- Entwicklung eines industriell anwendbaren Feuerfestkonzeptes
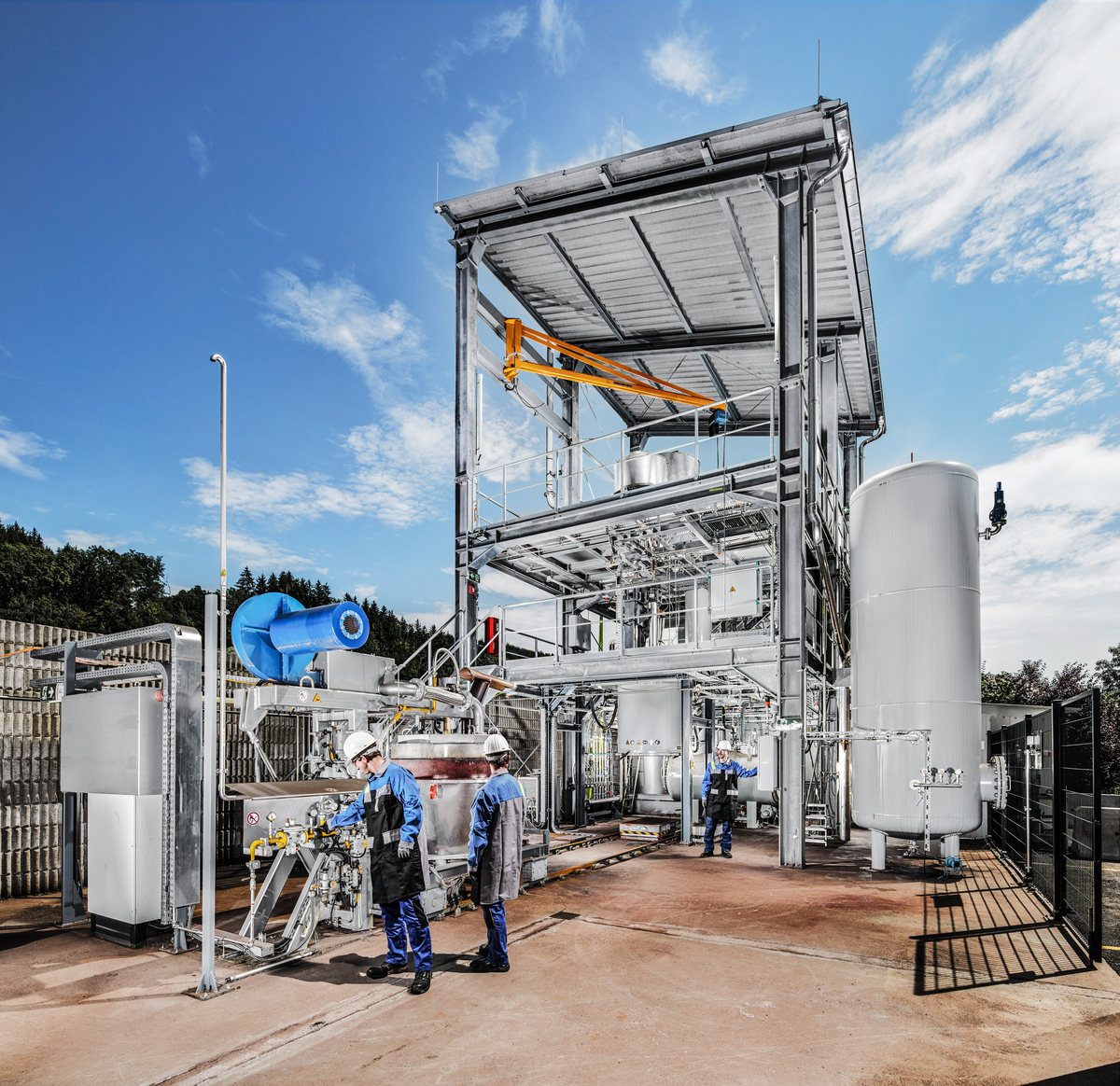
Vorgehensweise
- Literaturstudien, Entwicklung einer Theorie für das Verhalten von Begleitelementen mithilfe von thermodynamischen Simulationen
- Labor- und Pilotanlagenversuche unter verschiedenen Parametern zur Bewertung des Verhaltens von Begleitelementen
- Versuchskampagnen für den Einsatz von Oxiden als Legierungselemente und Entwicklung einer Stahlherstellungsroute mit HPSR als Kernreduktionsaggregat
- Versuche im Labormaßstab mit verschiedenen Setups zur optimalen Anordnung der Apparatur hinsichtlich des elektrischen Feldes und des damit verbundenen induzierten Stromes
- Entwurf eines Multikathodensystems für Versuche im Labormaßstab und dessen Versuchskampagnen
- Zusammenführung des Konzeptes und der Ergebnisse für den Beginn des Basic-Engineerings der Pilotanlage für einen kontinuierlichen Betrieb
- Entwicklung der CFD-Simulationsgeometrie und des Frameworks
- Vergleich der Simulationsergebnisse mit experimentellen Daten aus dem Reaktorbetrieb
- Festlegung des Zonenmodells für die Pilotanlage
- Versuche an den Labor- und Pilotanlagen zur Bewertung der Eignung verschiedener Feuerfestkonzepte in unterschiedlichen Zonen
- Pre-Engineering eines Feuerfestkonzeptes für die Pilotanlage
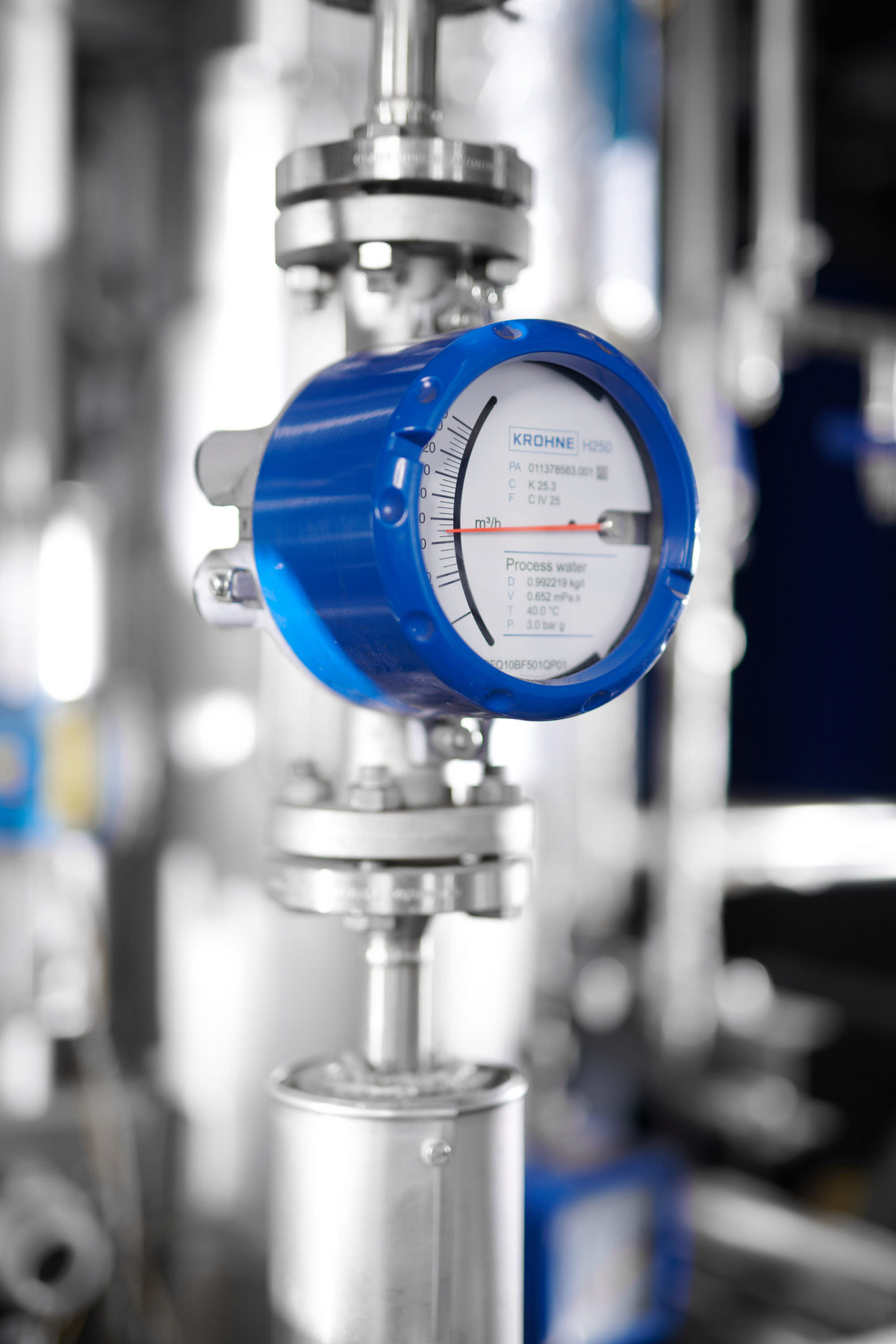
Ergebnisse und Anwendung
Das Projekt umfasst die Entwicklung eines Konzepts für die sich an den HPSR-Prozess anschließende Sekundärmetallurgie. Es wird ein Modell erstellt, um das Verhalten von Begleitelementen im Prozess zu analysieren. Der optimierte Einsatz von Oxiden als Legierungselemente wird untersucht. Es wird ein Verteilungsmodell für Phosphor und Schwefel bei verschiedenen Prozessbedingungen entwickelt.
Außerdem wird das optimale Design für die Anordnung der elektrischen Ausrüstung in der Pilotanlage ermittelt. Das beste Multikathodensystem für den Einsatz in der Pilotanlage wird ausgewählt. Die optimale Geometrie des Pilotreaktors wird bestimmt, um eine hohe Energiedichte und geringe thermische Verluste zu gewährleisten.
Es wird ein detailliertes Prozessfließbild vorbereitet und eine komplexe Massen- und Energiebilanz für die Pilotanlage erstellt. Die Schlüsselausrüstung der Pilotanlage wird bestimmt.
Der HPSR-Prozess und der Reaktor werden modelliert, um Prozesswissen zu gewinnen. Es werden Simulationsstudien unter verschiedenen Betriebsbedingungen und bei unterschiedlichen Prozessvariationen durchgeführt. Ein mehrschichtiges Konzept für die feuerfeste Auskleidung der Pilotanlage wird entwickelt. Darüber hinaus wird ein Konzept für das optimale Feuerfestmaterial in allen Prozesszonen entwickelt.