Projekt 3.3
Advancement of simulation acceleration for process applications (A.S.A.P.)
Einleitung
Die Beschleunigung von Simulationen ist ein Schlüssel zur Verbesserung von metallurgischen Prozesssimulationen, da diese häufig große Zeitspannen oder Geometrien und damit erhebliche Rechenkosten beinhalten. Das übergreifende Ziel dieses Projektes ist es, an der Weiterentwicklung von Simulationsmethoden zu arbeiten und zu einer besseren praktischen Anwendbarkeit von CFD-, DEM- oder FE-Simulationen beizutragen.
Im Bereich der CFD-Simulationen ist die Weiterentwicklung von „Recurrence CFD“ (rCFD) geplant. Ziel ist es, einen anwendbaren Workflow von State-of-the-Art-CFD-Simulationen hin zu echtzeitfähigen rCFD-Simulationen zu etablieren, die im Rahmen der letzten Förderperiode entwickelt wurden. Darüber hinaus werden weitere Methoden für neue, lokal beschleunigte Simulationsalgorithmen erprobt, die den Schwerpunkt auf einer automatisierten Suche nach rekurrenten Mustern auf lokaler Ebene legen, z.B. mittels Fourier-Methoden. Im Falle der FE-Simulationen wird die Entwicklung einer numerischen Methodik zur Beschleunigung von Feststoff-Simulationen von Feuerfestmaterial durchgeführt, die auf maschinellem Lernen basiert. Dabei wird auf die zukünftige Realisierung eines digitalen Zwillings von Auskleidungssystemen aus Feuerfestmaterial hingearbeitet.
Ziele und Motivation
- Erstellung einer Serie von CFD-Simulationen der Mehrphasenströmung in gängigen metallurgischen Prozessen als Validierungsbasis für neuartige rCFD-Simulationen, um die Möglichkeiten und noch bestehenden Grenzen dieser Methode zu erkunden
- Anpassungen und Weiterentwicklungen von rCFD im Rahmen einer gründlichen Überprüfung der Simulationsergebnisse (möglicherweise erforderliche Kalibrierung von lokalen Diffusions- und Quelltermen)
- Anwendung des neuen rCFD-Workflows auf metallurgische Prozesse von Argon-Sauerstoff-Entkohlungsprozessen im Konverter bis zu Strömungen im Strangguss-Gießrohr und -Verteiler
- Lokale Beschleunigung von Simulationsalgorithmen unter Berücksichtigung von wiederkehrenden Mustern auf lokaler Ebene, d. h. pro Zelle oder pro Bereich, anstatt auf dem gesamten Berechnungsgebiet
- Untersuchung von CFD-Strömungen in einfachen Geometrien als Anwendungsfall für die frühe Entwicklungsphase, sowie Vergleich und mögliche Kombination mit rCFD-Ergebnissen
- Anwendung verschiedener maschineller Lerntechniken für eine optimierte Vorhersage der Randbedingungen für die nächste Stufe der Finite-Elemente-Modellierung
- Entwicklung eines einheitlichen Modells der Materialzusammensetzung, das die gleichzeitige Beschreibung des irreversiblen Verhaltens unter Zug- und Scherspannung sowie Kriechdehnung ermöglicht
- Untersuchung des Ruhrstahl-Heraeus (RH)-Entgasungsgefäßes und Anleitung zur Optimierung der Auskleidung mit Feuerfestmaterial
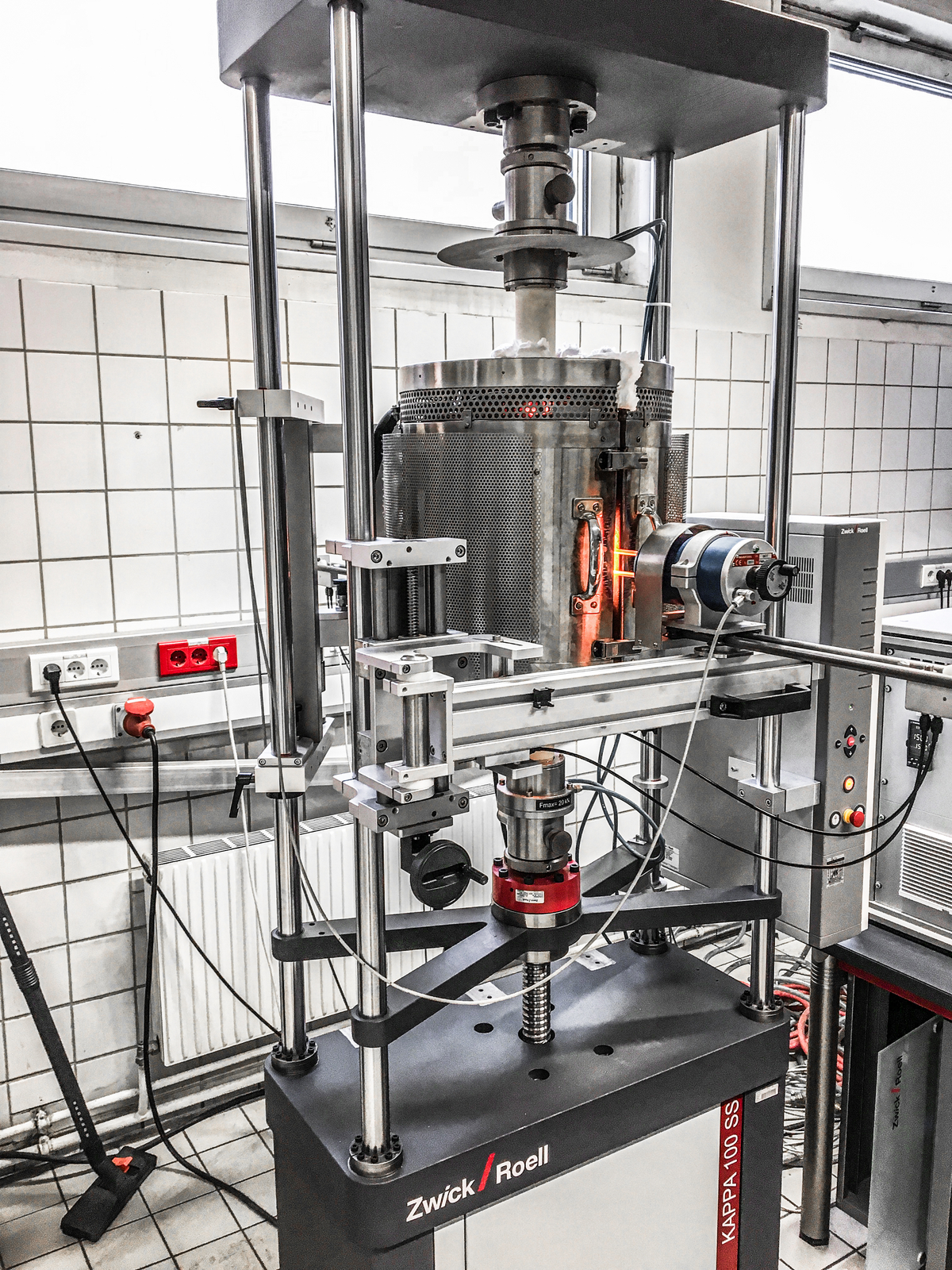
Vorgehensweise
- Mehrphasige CFD- und rCFD-Simulationen für verschiedene Betriebsbedingungen und geometrische Konfigurationen
- Validierung von rCFD-Simulationen durch numerische Experimente
- Spektralanalysen für abhängige Simulationsvariablen (Druck, Geschwindigkeit, Turbulenzvariablen usw.) mittels Fast Fourier Transformation (FFT)
- Einsatz von maschinellem Lernen zur Optimierung der FFT-Implementierung und Aufbau eines hybriden Simulationsmodells zur lokalen Beschleunigung von CFD-Simulationen
- Einsatz der Finite-Elemente-Methode (FE) und des maschinellen Lernens (ML) für die Projektarbeit
- Entwicklung von Modellen der Materialzusammensetzung für Auskleidungen aus Feuerfestmaterial und Implementierung in das kommerzielle FE-Programm ABAQUS
- Anwendung des einheitlichen Materialmodells bei der Simulation eines ausgewählten Auskleidungskonzeptes (Stabilitätsuntersuchung der Methodik und Optimierung der Auskleidung)
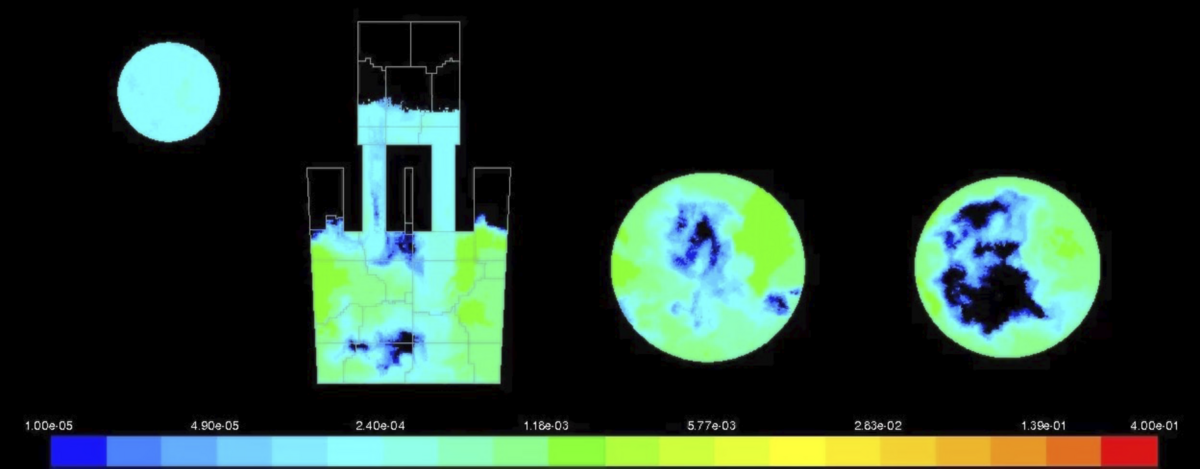
Ergebnisse und Anwendung
Im Hinblick auf die Anwendung von rCFD soll ein besseres Verständnis über die Anwendbarkeit von echtzeitfähigen rCFD-Simulationen im Bereich metallurgischer Prozesse gewonnen werden. Im Rahmen des Projekts sollen rCFD-Simulationen durch automatisierte Kalibrierungsroutinen der lokalen Diffusions- und Quellterme verbessert werden. Darüber hinaus wird dieses Projekt die Möglichkeit bieten, Echtzeitsimulationen von industriellen Prozessen zu etablieren und damit den Weg für neue Technologien zur Prozessbeobachtung und -steuerung zu ebnen.
Das Hauptziel der lokal beschleunigten Simulationsmethoden ist nicht die Prozessüberwachung in Echtzeit, sondern die Schaffung einer robusten und einfach zu handhabenden hybriden Simulationsmethode unter Verwendung von FFT oder anderer Methoden. Die Berechnung in bestimmten Bereichen (oder von bestimmten Variablen), die nicht von primärer Bedeutung sind, wird durch die Implementierung der hybriden Simulationsmethode beschleunigt und mit einem maschinellen Lernprozess optimiert. Die konventionelle CFD-Methode ist währenddessen weiterhin bei wichtigen Bereichen oder Variablen aktiv.
Das wichtigste technische Ergebnis der Beschleunigung von FE-Simulationen ist die Beschleunigung und Verbesserung der Simulation und Vorhersage des Feuerfestverhaltens. Darüber hinaus werden Anhaltspunkte für die Optimierung der Auskleidung und die Verbesserung der Nachhaltigkeit der Auskleidung gewonnen. Die Ergebnisse werden ein erster Schritt zur Erstellung eines digitalen Zwillings für das Verhalten der feuerfesten Auskleidung und die vorausschauende Instandhaltung sein. Die wissenschaftlichen Ergebnisse werden ein einheitliches Materialmodell sowie eine Methodik liefern, die FE- und ML-Ansätze für die Vorhersage des thermomechanischen Verhaltens von Auskleidungen kombiniert und Richtlinien für ihre Anwendbarkeit in anderen Simulationsmethoden enthält.
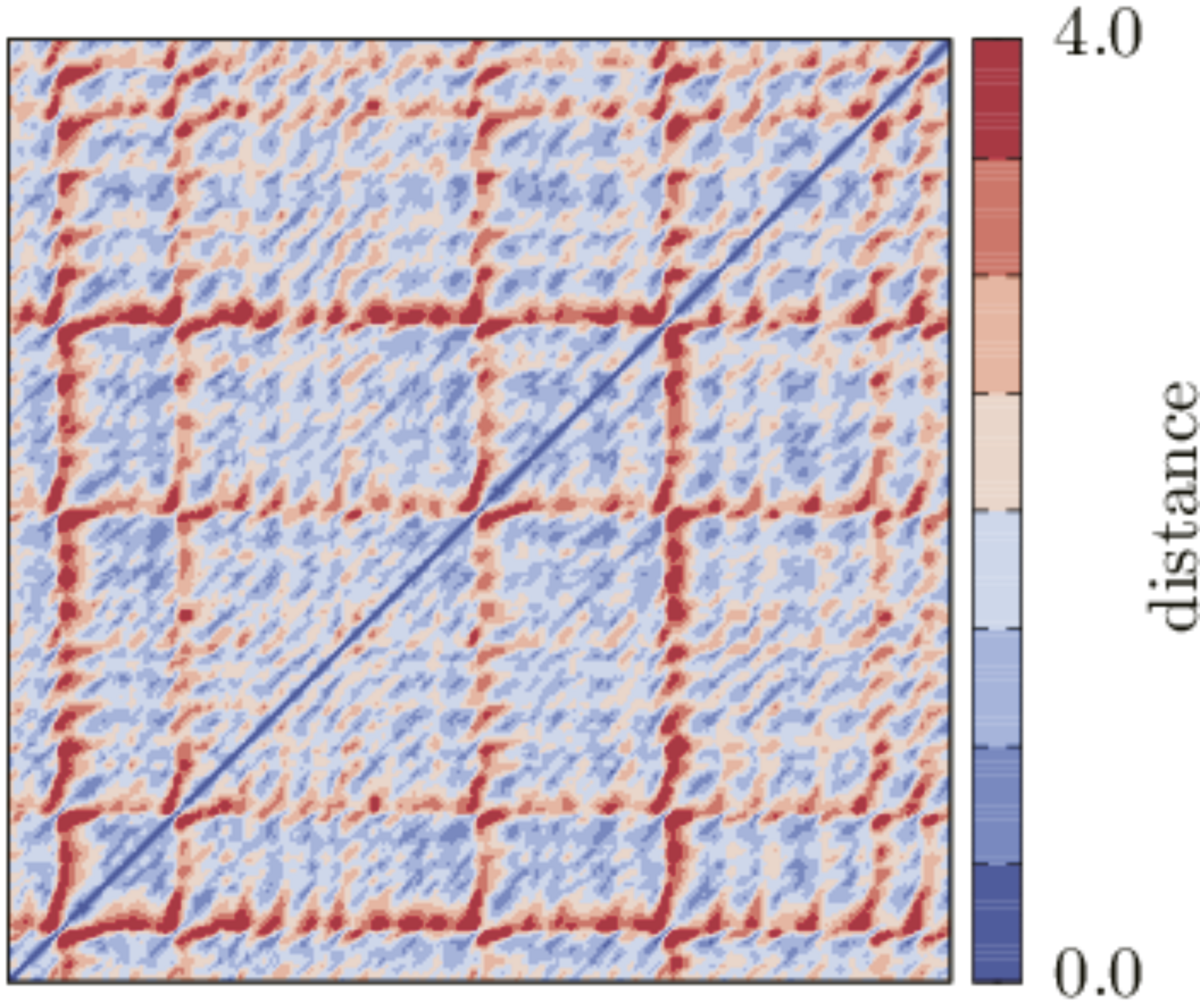