Projekt 3.1
Metallurgy-driven multiphase fluid modelling and simulation
Einleitung
Ziel dieses Projekts ist es, ein umfassendes Verständnis der physikalischen Mechanismen der Wechselwirkungen metallurgischer Mehrphasenströmungen zu erlangen. Dabei werden unterschiedliche Phasen wie flüssiges Metall, Schlacke, Gasinjektion, nichtmetallische Partikel und feste Wände aus Feuerfest-Material berücksichtigt. Numerische Studien werden durchgeführt, um metallurgische Prozesse in der Stahlherstellung besser zu verstehen, und eine Reihe experimenteller Untersuchungen werden eine Validierung für die numerische Modellierung liefern. Betrachtet werden Prozesse wie etwa der Konverter, sekundärmetallurgische Behandlungen und der Strangguss.
Blasenbeladene Strömungen sind eine wichtige Methode in der Stahlproduktion, um die Homogenisierung von flüssigem Metall zu verbessern, Verstopfungen zu verhindern und unerwünschte Elemente im Stahl zu entfernen. Um die Physik der Wechselwirkung zwischen flüssigem Metall, nichtmetallischen Einschlüssen (NMIs) und Gasblasen zu untersuchen, werden Phänomene wie die Bildung von Blasen und Blasenschwärmen sowie das Partikelverhalten in Blasenströmungen mit leichter und massiver Gasinjektion berücksichtigt. Darüber hinaus werden Partikelablagerungs- und Verstopfungsmechanismen sowie das Verschleißverhalten des Feuerfestmaterials in metallurgischen Reaktoren untersucht. Diese wichtigen Phänomene beeinflussen die Stahlqualität bei sekundärmetallurgischen Behandlungen und beim Strangguss wesentlich.
Das Projekt wird neuartige Modellierungsansätze nutzen und so die Präzision der Prozessdarstellung und das Prozessverständnis verbessern. Begleitend zur numerischen Modellierung wird die Analyse von Materialproben zur Validierung dieser Modelle und zur Bestimmung von wichtigen Modellparametern für die Simulationen dienen. Das Verhalten von Einschlüssen in der Grenzfläche von Stahl und Schlacke sowie deren Benetzungseigenschaften werden experimentell untersucht und unterstützen so Simulationsaktivitäten. Experimentelle Daten aus dem Anlagenbetrieb und von kleineren Laboraufbauten dieser Prozesse werden weiter zu einer Validierung der numerischen Untersuchungen beitragen.
Ziele und Motivation
- Erstellung umfassender Modelle von Prozessen der Stahlherstellung mit numerischen Simulationen (Computational Fluid Dynamics, CFD)
- Validierung numerischer Ergebnisse durch den Einsatz physikalischer Modellierung und Daten aus experimentellen Versuchsaufbauten
- Berücksichtigung von Blasenbildung und Partikelflotation, Fluid-Fluid-Wechselwirkungen, Gas-Fluid-Wechselwirkungen an der Blasengrenzfläche sowie Fluid-Feuerfestmaterial-Modellierung
- Untersuchung des Verhaltens nichtmetallischer Einschlüsse und Verstopfungsmechanismen
- Modellierung von Erosions- und Verschleißprozessen des Feuerfestmaterials
- Anwendung der Modelle auf den Argon-Sauerstoff-Entkohlungskonverter (AOD), den Ruhrstahl-Heraeus (RH)-Prozess und die Flüssigkeitsströme im Verteiler, Gießrohr (SEN) und Kokille
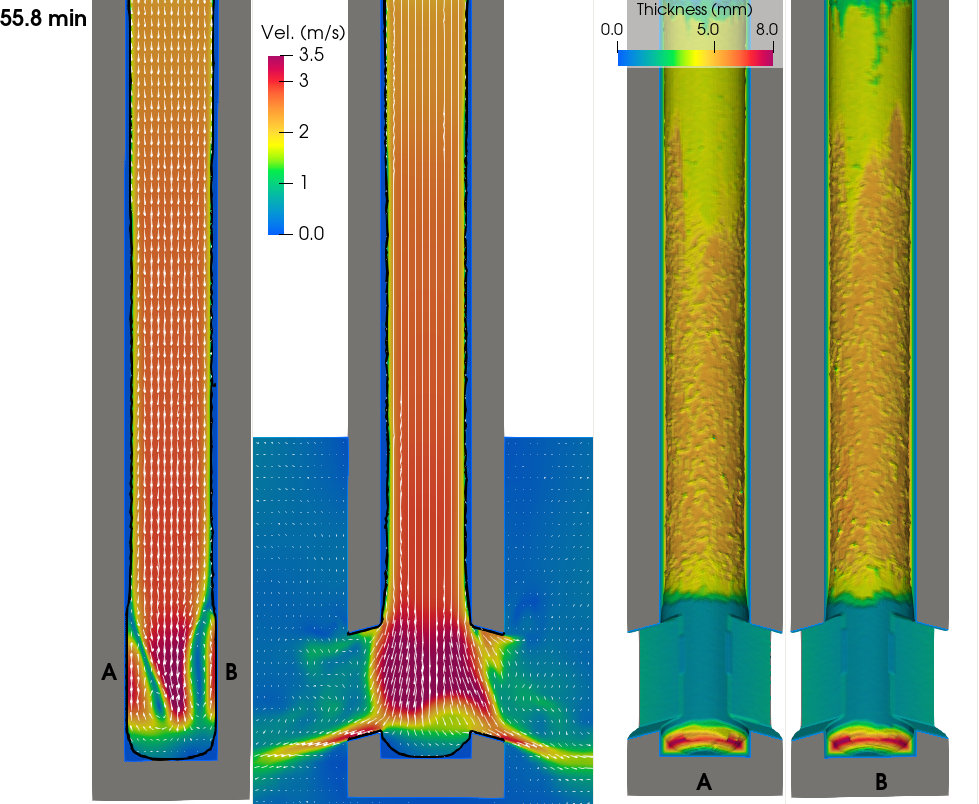
Vorgehensweise
- Untersuchung der Bildung von Blasen- und Blasenschwärmen sowie der Partikel-Blasen-Wechselwirkung durch analytische Überlegungen, hochaufgelöste numerische Simulation und Experimente, z.B. Aufnahmen und Analysen von Laborexperimenten mit Hochgeschwindigkeitskameras
- Erweiterung der Simulationsmodelle für Gießrohrströmungen in Hinblick auf Temperatureffekte und ihre Auswirkung auf Verstopfungen durch Berücksichtigung von Mehrphasenströmungen
- Entwicklung von physikbasierten numerischen Modellen kombiniert mit datengetriebenen Techniken des maschinellen Lernens
- Modellierung eines Erosionsgesetzes für Feuerfest-Material mit invers bestimmten Parametern, verifiziert durch Laborexperimente mit dem Continuous Wear Testing Device (CWTD)
- Untersuchung des Verhaltens spezifischer NMIs im System Stahl-Schlacke-Feuerfestmaterial mit verschiedenen Methoden wie Rasterelektronenmikroskopie (REM), energiedispersiver Röntgenspektroskopie (EDS), In-situ-Experimenten mit konfokaler Hochtemperatur-Laser-Rastermikroskopie (HT-LSCM) sowie Kontaktwinkelmessungen
- Physikalische und experimentelle Simulationen unter Verwendung verschiedener Stranggussmodelle (mit Verwendung von Wasser oder niedrigschmelzender Bismut-Zinn-Legierung in unterschiedlichem Maßstab) sowie eines RH-Anlagenmodells mit Wasser zur Validierung von Simulationen für verschiedene Prozessbedingungen
- Durchführung von Experimenten an industriellen Anlagen (z. B. Temperaturmessung im Gießrohr) und Anwendung von Data Mining für verstopfungsrelevante Parameter (z. B. metallografische Analysen und Laboruntersuchungen an industriell eingesetzten Anlagenteilen)
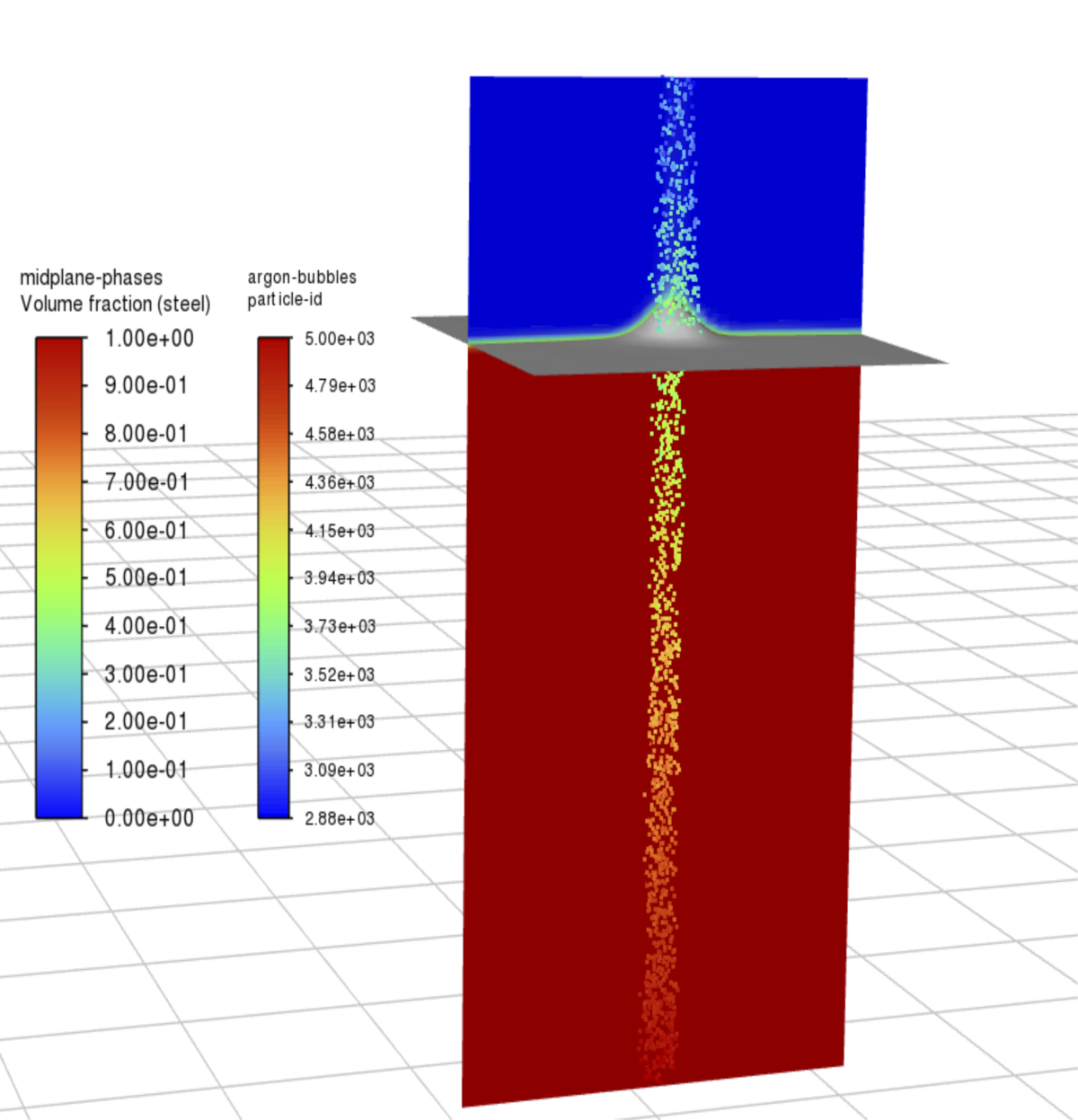
Ergebnisse und Anwendung
Durch die Forschungsaktivitäten werden Einblicke in das Verhalten von Blasen und Blasenschwärmen in Metallflüssigkeiten sowie in die Flotation von Partikeln und deren anschließende Trennung in Richtung der Schlackenphase oder Auswirkungen auf Verstopfungen gewonnen. Ursachen für das Verstopfen von Gießrohren und die daraus resultierende thermische Reaktion des Gießrohrs werden für verschiedene Stahlsorten und mit dem Einfluss von Temperaturen untersucht, unter Berücksichtigung physikalischer und chemischer Phänomene, die zwischen flüssigem Stahl und feuerfestem Material auftreten. Diese Ergebnisse werden in bestehende Verstopfungsmodelle für metallurgische Prozesse integriert.
Darüber hinaus wird die massive Injektion von Prozessgas unter Berücksichtigung der Kompressibilität und des Gasblasenverhaltens unter normalem und reduziertem Umgebungsdruck untersucht. Basierend auf diesen Erkenntnissen werden Lösungen für einen stabilen AOD-Betrieb und einer effizienten Umwälzung im RH-Prozess erwartet.
Die Phänomene des kontinuierlichen Feuerfestverschleißes werden untersucht und quantifiziert, um materialbezogene Verschleißparameter zu erhalten. Das Wissen über den Verschleiß feuerfester Materialien wird zur Entwicklung neuer feuerfester Materialien beitragen, die in verschiedenen industriellen Prozessen verwendet werden können, wodurch nicht nur Kosten, sondern auch der Verbrauch von Rohstoffen und Energie, und die Menge des Verschleißmaterials reduziert werden können.
Durch die Untersuchung des Fließverhaltens von flüssigen Metallen werden numerische Simulationen der Kokillenströmung in Stranggussanlagen erstellt, mit dem Ziel, Prozessparameter zu optimieren. Simulationsergebnisse werden durch Messungen an physikalischen Modellen mit Wasser oder niedrigschmelzenden Metalllegierungen validiert und verfeinert, mit dem Ziel, experimentelle Ergebnisse in CFD-Modelle zu übertragen. Abschließend werden Simulationsergebnisse für reale Industrieprozesse angewandt und analysiert, um die Relevanz der Simulation für eine verbesserte Prozesssteuerung und Prozessüberwachung zu beurteilen.
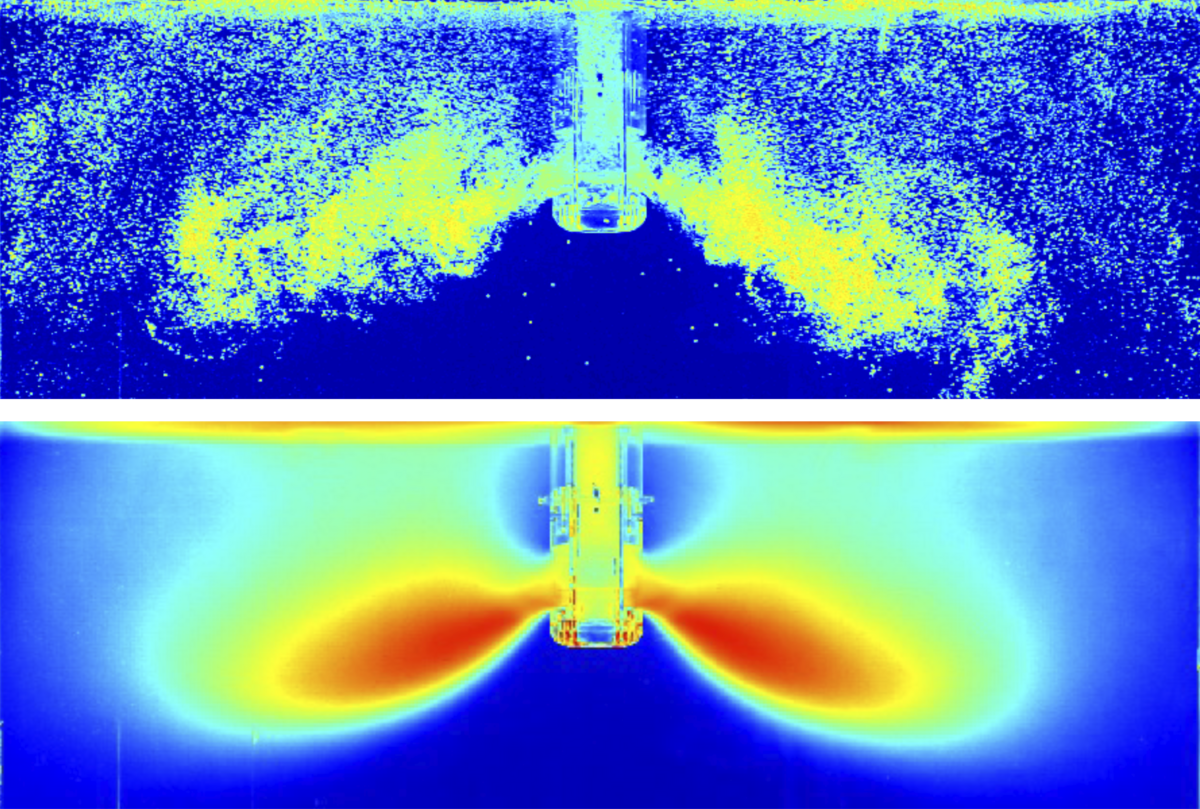