Project INNOMET
Innovative treatment of metallurgical dusts and slags by means of leaching and separation for the recovery of metallic secondary raw materials
Overall approach
Zinc-containing steel mill dusts and slags generated during iron and steel production via the route Blast Furnace – Basic Oxygen Furnace route or in the Electric Arc Furnace (EAF), can be considered as significant secondary raw materials. Currently, two processes are state of the art regarding the separation and recovery of zinc from steel mill dusts, namely pyrometallurgical and hydrometallurgical processes. However, some process routes in turn generate non-recyclable secondary waste and, in some cases, can only be operated at high cost and therefore cannot be classified as sustainable from an ecological point of view. The Waelz process (rotary kiln process) and the INMETCO process (direct reduction process in a shaft furnace) are two pyrometallurgical processes that exist on a large scale. A global shift in thinking towards circular economy, as well as declining landfill capacities and considerable disposal costs, are leading to increasing interest in innovative reprocessing concepts for steel mill dusts and slags with a high zinc content. An innovative, environmentally friendly, and energy-efficient approach here is biological metal recovery from dusts and slags (= bioleaching). Bioleaching is a naturally occurring, microbial process in which various metals are dissolved from ores or other metal-bearing materials through the formation of organic and inorganic acids, oxidation and reduction reactions and the precipitation of complex-forming substances.
Optimized metal recovery from metallurgical residues (dusts and slags) should be achieved in the INNOMET project by a semi-continuous treatment combination of biological leaching (bioleaching) by microorganisms and downstream metal recovery (bioelectrochemical separation or fractional precipitation). In addition, a leaching process using deep eutectic solvents was tested. Leaching processes, such as bioleaching, offer energy-saving methods (atmospheric pressure, low to moderate temperatures) to dissolve metals from oxide solid mixtures. By suitably coupling leaching with selective separation mechanisms, metal fractions can be recovered in refined form.
Objectives
The INNOMET project aimed at an optimized metal recovery from metallurgical residues (dusts and slags). The focus was on obtaining an iron-rich secondary raw material, which can be recycled into the steel mill process. The residual materials investigated in the project were blast furnace dust and casthouse dust produced in the blast furnace process, dust from the electric arc furnace, and slag from the BOF generated in the steelmaking process. The objectives of INNOMET were:
- Combined consideration of bioleaching and subsequent metal recovery to produce iron-rich secondary products and a non-ferrous metal alloy.
- Use of deep eutectic solvents for leaching of steelmaking slag for selective and energy-saving phosphorus recovery in the form of phosphates
- Special mixtures of fine-grained metallurgical residues (dusts from process gas cleaning) for a sustainable and efficient treatment of one or more residue streams coming from a steel mill process
- Evaluation of possible CO2 reduction potentials by replacing crude ore for primary production by the iron-rich secondary products
Framework
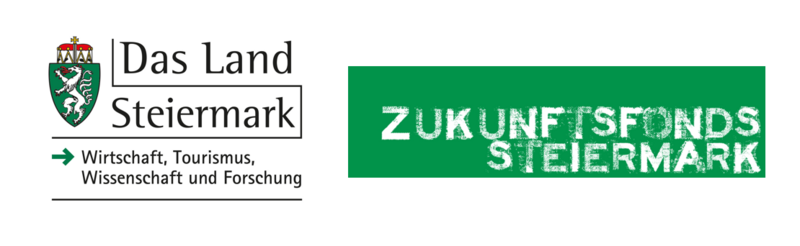
Project timeline:
2023-01-01 to 2024-12-31
Funding scheme:
This project was funded by the Province Styria (Zukunftsfonds Steiermark) (Grant Agreement no. PN 1507).
Project consortium:
Beginning with the project coordination, the consortium was formed as follows:
- K1-MET GmbH
- Montanuniversitaet Leoben – Chair of Ferrous Metallurgy
- Montanuniversitaet Leoben – Chair of Process Technology and Environmental Protection