Project TransZeroWaste
TransZeroWaste – Upgrading of low-quality iron ores and mill scale with low carbon technologies
Overall approach
Iron ore and scrap as raw materials provide the foundation for iron and steel production. The transition from carbon-based to green steel production with H2 will replace the current production facilities such as sinter plant, blast furnace and basic oxygen furnace with a direct reduction process followed by the electric arc furnace. Consequently, the current recycling paths for mill scale are eliminated and enhances the demand for high quality direct reduction pellets and scrap, turning them into critical factors. TransZeroWaste is addressing the technological and time requirements of the European steel industry in order to develop and demonstrate application-oriented results and technologies for the upgrading of low-grade iron ore at an early stage.
TransZeroWaste supports the development of low-carbon technologies such as cold pelletizing and briquetting, hot microwave pelletizing and magnet-assisted hydrometallurgy from TRL 6 o TRL 8. The resulting solutions are expected to be transferable to other material flows such as dusts and sludges. The overall impact of TransZeroWaste includes processing 27 Mt/a of material with low-carbon technologies and avoiding of corresponding sinter plant carbon footprint of 4.3–9.9 Mt CO2/a.
Objectives
TransZeroWaste is developing solution concepts for upgrading low-quality iron ore and mill scale. This is achieved either by combining them with iron-rich by-products or by applying innovative methods to produce high-quality starting material for future decarbonized production routes. In addition, the separation of interfering components from by-products provides an alternative to scrap. The demand for iron ore pellets or scrap is decreasing and the zero-waste goal for important waste carriers or previously non-recycled scrap equivalents is achievable. An eco-design approach supports the development of these technologies. It examines the environmental impact using LCA methods and identifies the key influencing factors and the most sustainable design alternatives. The objectives of the TransZeroWaste project are:
- 10–20 % upgrade of ores with iron content < 60 % by adding treated iron-rich residuals
- Reduction of CO2 emissions and slag prevention by upgrading ores
- Transfer of TransZeroWaste techniques for de-oiling of ferrous material to conventional scrap application
- Low-grade ore pellets directly usable for fluidized bed direct reduction process through TransZeroWaste processing
Framework
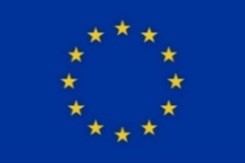
Project timeline:
2022-12-01 to 2026-11-30
Funding scheme:
This project has received European Union’s Horizon Europe research and innovation funding (Grant Agreement no. 101091960).
Project consortium:
Starting with the project coordination, the consortium is composed as follows:
- Luxembourg Institute of Science and Technology
- Agencia Estatal Consejo Superior de Investigaciones Científicas
- Aktiengesellschaft der Dillinger Hüttenwerke
- Compania Espanola De Laminacion SL (CELSA Group)
- ESTEP Plateforme Technologique Europeene de l’Acier
- INNCEINMAT S.L.
- Instituto de Soldadura e Qualidade (ISQ GROUP)
- K1-MET GmbH
- Proigmenes Erevnitikes & Diahiristikes Efarmoges
- Siec Badawcza Lukasiewicz – Instytut Metalurgii Zelaza im. Stanislawa Staszica
- Universitat Politecnica de Valencia
- VDEh-Betriebsforschungsinstitut GmbH