Project MinSiDeg
Minimise sinter degradation between sinter plant and blast furnace exploiting embedded real-time analytics
Overall approach
The integrated BF route is still the dominant steel production route in Europe and sinter is one of the most important iron sources within this route. The sinter plant offers the unique capability to recycle residues into the steel production and, even more important, provides high flexibility with respect to the raw materials and the product specifications required for the blast furnace. Due to rising prices and limited availability of high-quality ores, the European steel industry is under increasing pressure to use ores of lower quality (with respect to grain size distribution or composition). At the same time, the political and economic demands to decrease energy consumption and emissions are getting stronger.
Correspondingly, the performance of sinter plants is a crucial factor in cost and energy optimization. On one hand, the quality of the sinter depends on the raw materials and the operation of the plant, which in many cases is limited by external factors such as availability of resources and blast furnace demands. On the other hand, the sinter quality can also be influenced substantially by the material handling following the production, i.e., on the way from the sinter strand to the blast furnace. Figure 1 depicts the most important sources of stress for sinter degradation until its destination at the blast furnace.
Therefore, increased effort must be made to improve sinter plants’ output, and particular focus should be placed on the elements connecting sinter plants with other aggregates of a steel plant. Both the sinter process itself and the blast furnace process have individually been optimised for decades, so further increase of resource and energy efficiency is laborious. Thus, MinSiDeg planned to exploit the rarely considered improvement potential at the interlink of those two processes.
In MinSiDeg, several innovative online methods for continuous sinter quality monitoring were established, combined and evaluated with new embedded real-time tools for machine supported quality control. The degradation during transport could be minimised by new transfer systems. As a result, the losses due to transport are expected to decrease and stable high-quality sinter will be produced at low costs and energy consumption.
Objectives
A major objective of the project MinSiDeg was to improve cost and energy efficiency of sinter plants and blast furnaces. To achieve this, the sinter quality was optimised along the production chain improving both, sinter plant, and blast furnace operation.
The first step was to establish quantitative information on sinter quality fluctuations, considering the current status quo, and intensifying the exploitation of data by Big Data methods. Further, the sinter degradation by material handling was minimized by making physical sinter quality more transparent throughout the process and subsequently improving the handling in crucial process steps, in order to provide high quality sinter to the blast furnace and ensure good blast furnace shaft permeability.
MinSiDeg realised these objectives by 3 main approaches:
- Online monitoring of physical sinter quality by new measurements and data evaluation methods.
- New equipment and material handling procedures along the transfer to the blast furnace in order to decrease losses and stabilize sinter quality.
- Real-time analytics of existing and new data streams for machine supported decisions via Big Data technologies and digitalization.
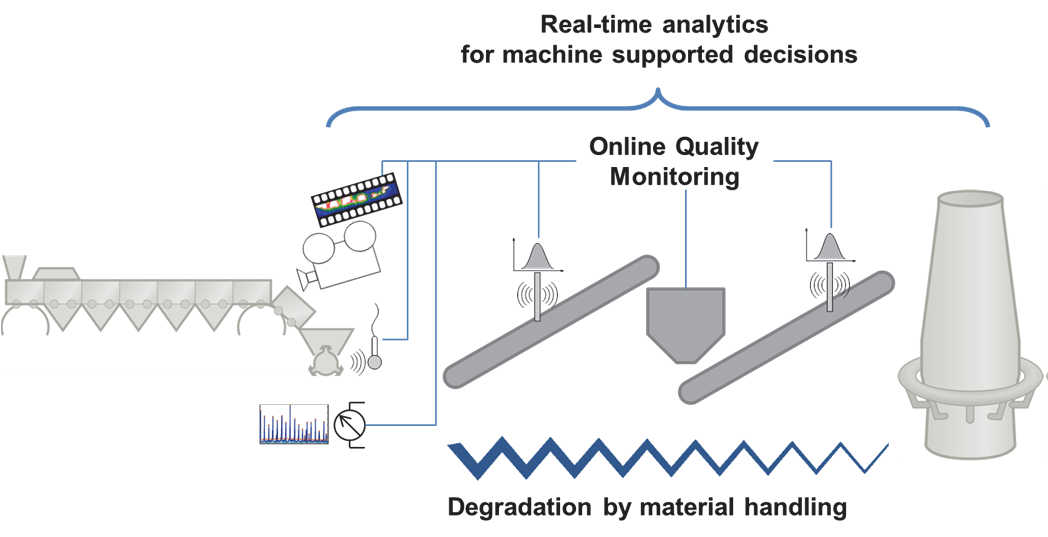